Mooney Viscometer GT-KR03— Your Comprehensive Guide
In the world of rubber manufacturing, ensuring quality and consistency in raw and compounded rubber is critical. This is where the Mooney Viscometer GT-KR03 comes into play. A sophisticated yet essential instrument, the Mooney Viscometer is designed to measure the viscosity and scorch characteristics of rubber materials.
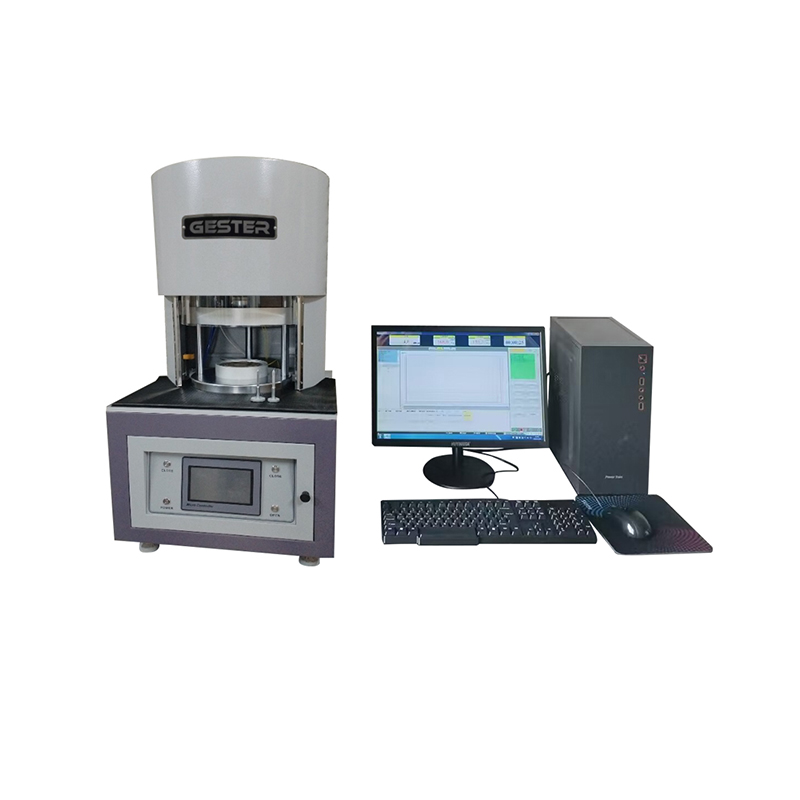
The Mooney Viscometer GT-KR03 is a state-of-the-art device used primarily in the rubber industry to determine the viscosity and scorch of both raw and compounded rubber. Viscosity, in this context, refers to the material’s resistance to flow under specific conditions, which plays a vital role in processing rubber. Scorch, on the other hand, indicates the tendency of rubber to undergo premature curing or crosslinking during manufacturing.
Key Applications of the Mooney Viscometer GT-KR03
The Mooney Viscometer is a versatile tool that plays a crucial role across a range of industries. Its primary application lies in rubber manufacturing, but it also extends its benefits to a variety of other sectors:
1. Rubber Manufacturing
Process Control: By measuring the viscosity and scorch characteristics, manufacturers can optimize the mixing and curing processes, ensuring a consistent and high-quality end product.
Quality Assurance: Ensures that raw rubber and compounded rubber meet industry standards, minimizing defects and ensuring performance reliability.
2. Footwear Industry
Material Optimization: In footwear production, the Mooney Viscometer helps manufacturers assess rubber compounds used in soles and other components, ensuring durability, comfort, and functionality.
3. Automotive Industry
Engine Components and Tires: The performance of rubber materials in automotive parts, such as tires and seals, is highly dependent on their viscosity and scorch characteristics. The Mooney Viscometer helps ensure that the rubber compounds used in these applications meet the required specifications.
4. Construction and Mining
Durability Testing: Rubber used in construction materials, machinery seals, and mining equipment needs to withstand extreme conditions. The Mooney Viscometer ensures that the rubber compounds used in these environments possess the necessary properties for durability and performance.
5. Household and Transportation Items
Consistent Quality: Items such as rubber seals, gaskets, and hoses in household and transportation products benefit from the precision and consistency ensured by Mooney Viscometer testing.
6. Research and Development
Innovative Materials: The Mooney Viscometer is an essential tool in R&D settings, providing detailed data on the properties of new rubber formulations and allowing researchers to fine-tune compositions for specific applications.
1. Accurate and Precise Measurements
Our Mooney Viscometer is designed to deliver highly accurate readings of rubber viscosity and scorch, ensuring precise data for manufacturing and quality control purposes.2. User-Friendly Interface
Equipped with an intuitive interface, the rubber testing instrument GT-KR03 allows for easy operation and quick access to critical data. Its clear digital display provides real-time results, allowing operators to monitor changes in material properties during processing.
3. Durable Construction
Built to withstand the demanding environments of rubber production facilities, the Mooney Viscometer GT-KR03 is designed for long-term durability. Its rugged construction ensures reliability even in harsh operating conditions.
4. Versatility
This mooney viscosity machine is compatible with a wide range of rubber materials, making it suitable for use across different industries, from automotive to footwear to cons truction.
5. Improved Process Control
By providing detailed insights into the viscosity and scorch behavior of rubber, the Mooney Viscometer enables manufacturers to make informed adjustments to their processes, resulting in optimized material properties and enhanced product quality.
6. Efficient Data Management
The GT-KR03 rubber mooney viscosity offers advanced data management features, allowing for easy storage and retrieval of test results. This makes it an ideal tool for tracking performance over time and maintaining quality consistency.
By investing in the Mooney Viscometer GT-KR03, manufacturers gain a powerful tool for quality control, process optimization, and research and development—ensuring that their rubber products meet the demands of both today’s and tomorrow’s industries.